A Comprehensive Overview to the Kinds Of Ceramic Finish on the Market
Ceramic coverings have arised as a pivotal option throughout various sectors due to their special residential properties and applications. As we check out the unique attributes and applications of these coverings, the effects for performance and durability come to be progressively apparent, elevating inquiries regarding which type may best match your demands.
Understanding Ceramic Coatings
Ceramic layers are sophisticated protective solutions that have actually gained popularity in different sectors, particularly in automotive and aerospace applications. These layers consist of a liquid polymer that, when cured, develops a resilient, hydrophobic layer on the surface area of the substratum. This layer gives boosted resistance to environmental contaminants, UV radiation, and chemical exposure, therefore expanding the life and visual charm of the underlying product.
The basic element of ceramic finishes is silica, which adds to their solidity and durability. The application procedure usually includes surface preparation, application of the coating, and healing, which can be achieved via warmth or UV light. Once treated, ceramic finishes show exceptional bonding residential or commercial properties, allowing them to stick highly to a range of surfaces, including steels, plastics, and glass.
Along with their protective attributes, ceramic coverings also use ease of maintenance. Their hydrophobic nature lowers the adherence of dirt and grime, making cleaning simpler and much less constant. In general, the fostering of ceramic layers stands for a substantial improvement in surface defense innovation, providing both aesthetic and functional benefits across several markets.
Kinds Of Ceramic Coatings
Various kinds of ceramic coatings are offered, each designed to meet specific performance requirements and applications. The most common types consist of:
Silica-based Coatings, these coverings mostly are composed of silicon dioxide and are understood for their resilience and chemical resistance. They are extensively utilized in auto and industrial applications.
Titanium Dioxide Coatings: Renowned for their photocatalytic buildings, titanium dioxide layers are often applied in atmospheres where self-cleaning and antifungal residential or commercial properties are preferable, such as in building products and automobile surfaces.
Zirconia Coatings are defined by their high-temperature security and thermal resistance, zirconia finishings are used in applications such as wind turbine engines and high-performance auto components.
Alumina Coatings, Displaying superb hardness and thermal security, alumina coverings are often made use of in wear-resistant applications, consisting of reducing devices and industrial equipment.
Hybrid Coatings:Integrating the residential properties of numerous materials, crossbreed finishes provide boosted efficiency characteristics, making them appropriate for unique and demanding applications.
Each kind of ceramic layer serves distinct functions, enabling customers to select the most suitable solution based on certain ecological problems and efficiency needs.
Benefits of Ceramic Coatings

Along with sturdiness, ceramic coatings offer exceptional hydrophobic buildings, enabling simple cleansing and upkeep. This water-repellent nature decreases the adherence of dirt, grime, and various other contaminants, which can extend the aesthetic charm and capability of the surface area. Ceramic finishes can dramatically boost thermal resistance, making them perfect for applications that sustain high temperature levels.
An additional significant advantage is their ability to enhance surface area firmness. This raised solidity can cause reduced damage, eventually extending the lifespan of the layered product. Ceramic finishes can contribute to energy effectiveness by showing heat, which is particularly useful in commercial and auto setups. In general, the countless benefits of ceramic coverings make them an important financial investment for numerous applications, ensuring optimal performance and defense.
Application Process
When using ceramic layers, a thorough approach is important to achieve ideal results. The application process generally starts with comprehensive surface area prep work. This entails cleaning, decontaminating, and polishing the surface area to get rid of all impurities, consisting of dust, grease, and prior waxes or sealers. A clean surface makes sure correct adhesion of the finish.
When the surface area is prepped, the following step is to use the ceramic layer. This can be done making use of an applicator pad or a microfiber towel, making sure also coverage. It is essential to work in tiny sections to preserve control and avoid early treating - Ceramic Coating Denver. The read here finishing needs to be used in thin layers, as thicker applications can lead to unequal finishes.
After application, the finishing needs a particular treating time, typically varying from a few hours to a full day, depending on the item. Following these steps faithfully will make the most of the effectiveness and durability of the ceramic finish, giving a durable safety layer for the surface.
Maintenance and Longevity
To make try this sure the long life and performance of a ceramic layer, routine maintenance is necessary. Ceramic coatings, recognized for their longevity and safety top qualities, need particular care routines to maximize their lifespan and efficiency. The primary step in maintenance includes regular cleaning with pH-neutral soap, avoiding rough chemicals that can break down the covering. It is advisable to clean the automobile on a regular basis, preferably every two weeks, to avoid the accumulation of pollutants that might endanger the finishing's stability.
Along with regular cleaning, regular evaluations are critical. Look for indications of wear or damages, such as hydrophobic buildings decreasing or surface flaws. If required, a light polish may be applied to renew the coating without removing it away.
In addition, the application of a booster spray can improve the covering's hydrophobic impacts and restore its gloss. This is especially valuable for layers that have actually been in usage for an extensive period. Inevitably, by adhering to these upkeep techniques, one can dramatically prolong the life of a ceramic finish, making certain that it remains to provide optimal protection versus environmental factors and preserve the visual allure of visit here the automobile.
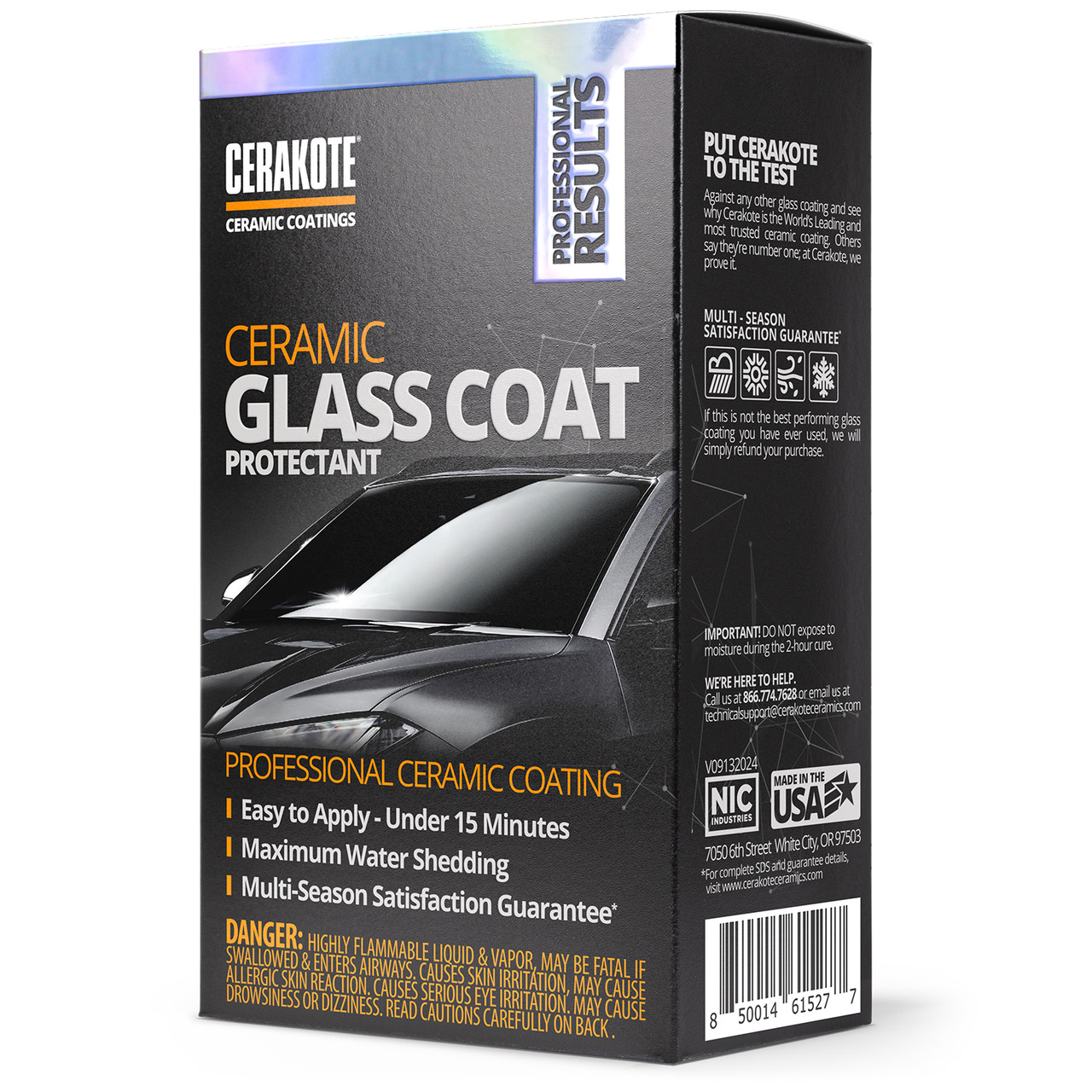
Final Thought
To conclude, ceramic finishings represent a versatile option for a series of applications, supplying a variety of types such as silica, titanium zirconia, alumina, and dioxide. Each type presents unique benefits, including durability, self-cleaning buildings, high-temperature security, and wear resistance. The application procedure and ongoing maintenance play essential roles in optimizing the durability and efficiency of these layers. In general, ceramic coverings contribute considerably to boosting the resilience and functionality of different surfaces throughout multiple sectors.
Ceramic coverings have emerged as a crucial service across different markets due to their distinct residential or commercial properties and applications.Ceramic finishings are advanced protective options that have actually obtained appeal in different sectors, especially in aerospace and automotive applications. Ceramic layers can substantially boost thermal resistance, making them optimal for applications that endure high temperatures.
Generally, the countless benefits of ceramic finishings make them a beneficial investment for numerous applications, ensuring ideal efficiency and protection.
In final thought, ceramic finishes stand for a functional remedy for a variety of applications, offering a selection of types such as silica, titanium alumina, dioxide, and zirconia.